Everybody had the opportunity to work on it. Nobody did more things than anybody else. We made sure everybody was on task.
MERCEDES — Teamwork.
Every student in Oscar Rodriguez’s agriculture mechanics class agreed they’d each worked together to build their award-winning squeeze chute, welding trailer and flatbed goose-necked trailer.
“It was a team project overall,” said Barrett Rabel, 17, a junior at Mercedes High School.
“We all worked together,” he emphasized. “Not one person did more than the other.”
Barrett and his three teammates began working on the flatbed trailer in late August and finished in early January, and their diligence paid off. The project took third place in the livestock equipment event at the Rio Grande Valley Livestock Show earlier this month.
Another three classmates built a welding trailer that took first place in that event. The second place went to the squeeze chute built by Jose Ruiz and Jesse Villalobos.
“It took us roughly 600 hours and six months, dedication after school and on the weekends,” said Jose, 18, a senior at Mercedes High School, who began working on welding projects for livestock show as a freshman.
The specific numbers — 600 hours and six months — convey the precise and detailed work required of shop students, not only in the measurements and the specifics of construction but in its delivery to shows.
Each project requires a detailed log showing the specific work performed at a stated time frame. This record serves as proof of the long hours of labor and technique employed by each student.
Their work served them well in not only the RGVLS but also at shows in Fort Worth, San Angelo, Houston and San Antonio.
They’ve definitely made a name for themselves, as revealed by all the awards on display in their shop.
“Reserve Champion, Southwestern Exposition and Livestock Show,” reads one. “Reserve Grand Champion, San Angelo. Division One Champion.”
Rodriguez expressed pride in his students’ success.
“It’s not a surprise for Mercedes kids,” he said. “They take their work and dedication seriously. It’s pretty presentable when we get to the shows.”
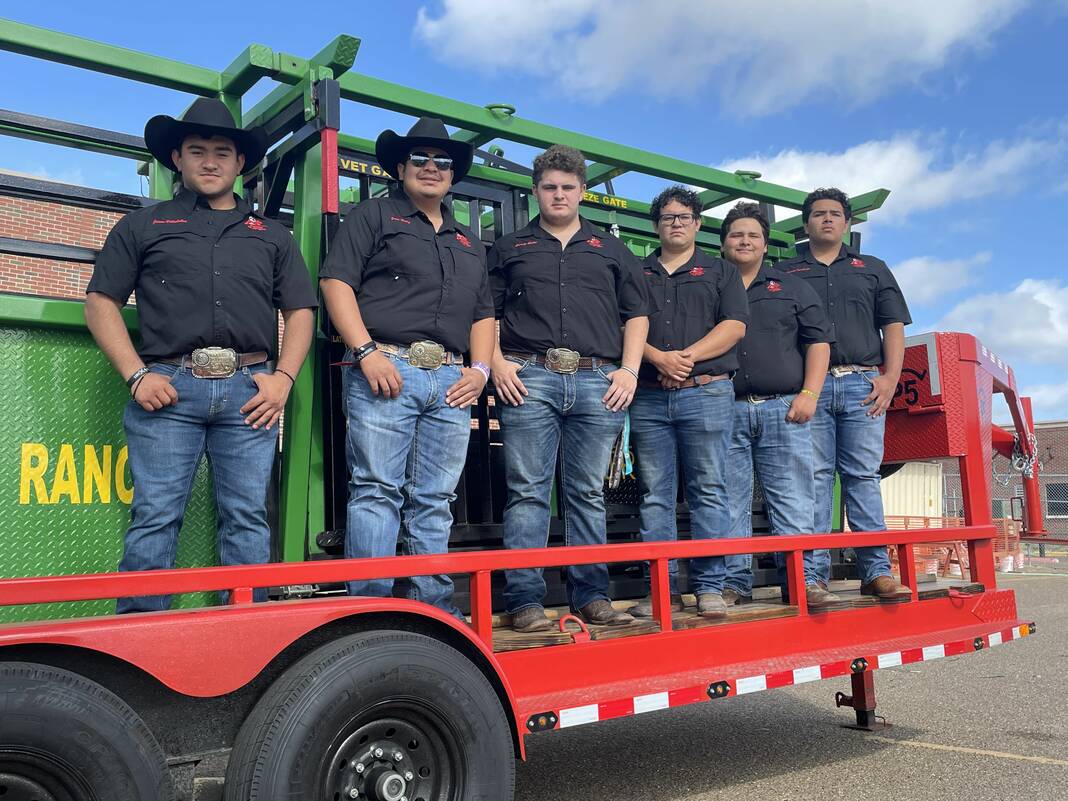
Jesse Trevino and his two teammates logged in 750 hours working on their welding trailer.
“It’s a little bit different from any of the other welding trailers in that it closes,” said Jesse, 16, a sophomore.
“The reason for that is our sponsor needed something he could lock up and not worry about it being stolen from,” Jesse said. “He wanted to be able to leave it at a job site or a hotel parking lot.”
The students built all three of their projects at the request of sponsors who paid for supplies.
While some gave very detailed specifications of what they wanted, the welding trailer sponsor gave the three-person team some room for creativity, which they seemed to enjoy.
“He didn’t really tell us how he wanted it,” Jesse said. “He let us figure that out. But we all just started throwing ideas at each other. We’d ask what he thought about it, and he’d tell us what he wanted to change on it.”
And the result?
“He’s seen it, and he loves it,” Jesse said.
Students creating such projects must employ a range of skills acquired over an extended period of time. The explanations they delivered about their work revealed an advanced expertise.
“We wire-brushed every inch of the metal,” said Luis Garza, 19, who worked on the flatbed.
“We welded it and created access for the trailer and a winch for towing,” Luis continued. “We added ramps for ATVs and small tractors and a toolbox for chains or for storage for drills or anything he needs, and lights to have a good view of the trailer.”
The most challenging part, Luis said, was framing the trailer correctly and according to detailed specifications. This attention to detail is vital for the success of a shop project, as the students will quickly emphasize.
Jose Ruiz said the squeeze chute on which he and Villalobos worked was the most difficult of his four years in shop class.
“We had a lot of angles. We had a lot of measurements, and everything needed to go right because if you go off by a little bit, you’re going to tell really quick,” he said. “You have to be precise.”
And of course, everyone must have that same capacity for precision work for the project to succeed.
“It was an equal opportunity of work,” said Jose Gonzalez, 17, who worked on the flatbed.
“Everybody had the opportunity to work on it,” he said. “Nobody did more things than anybody else. We made sure everybody was on task.”